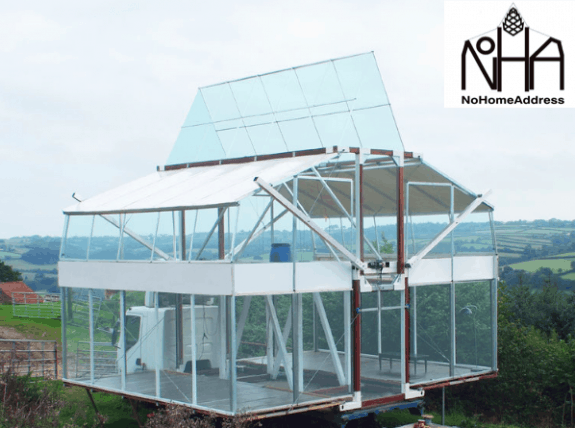
In a press release and video, Richard Perkin expresses what he calls his dream. That dream is for a happier, more exciting, and more “conscious way of life” with no environmental impact. It sounds great, because he says he is quitting his full time engineering job, and then sold his house to focus on it his project.
Its called NoHA Bios, and is on the Kickstarter funding site to further develop the prototype.
The Daily Business News routinely features 3D, prefab and modular concepts from around the globe, to keep systems- and factory-builders up-to-date one what’s trending, or up-and-coming.
But some of these projects lack key details, and that’s the case with NoHA. First, the Daily Business News will review the details from Perkin. Then, we’ll look at the questions from MHProNews that he did not answer.
The Designer’s Key Claims
The shipping container-sized unit is said to expand to a two story, 800 square foot house with a garden on the roof. It calls for a set of bespoke brackets to simplify the construction for do it yourself (DIY) assembly, with the rest of the structure comprised of structural timber and standard off-the-shelf materials and components to make it as affordable as possible.
The “not so tiny home,” costs around £16,000 ($19,947 USD) to build, aims to provide a truly independent and sustainable lifestyle, ultimately incorporating water, heating, refrigeration and food production along with waste reduction and recycling.
“I had a desire for minimalist surroundings, but would feel claustrophobic in a traditional tiny house – I’m 6’3” tall,” said Perkin.
“I wanted water without having to be connected to municipal services. I wanted a way to grow food all year round within arm’s reach. And I wanted ways to recycle all organic waste and to cook and heat with renewable energy sources…and for all of this to be incorporated into a transportable unit.”
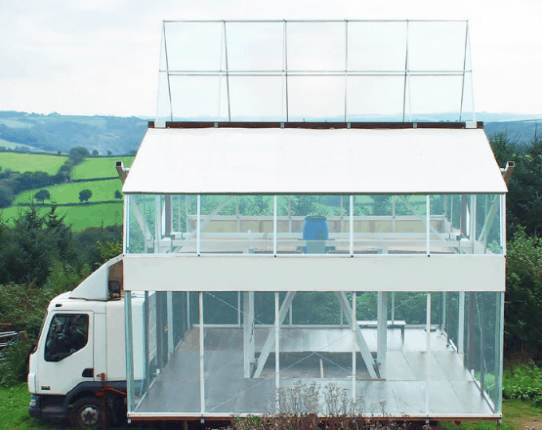
As the engineer-turned-architect looks for additional funding, he’s focused on his vision of making his homes available for everyone.
“The NoHA BiOS is a living platform designed to challenge the norms, to redefine the idea of a house as a home…a vision to create a spacious, light and airy structure that provides the benefits of mobile living without the limitations of mobile homes, and offers the advantages of traditional static homes without the associated costs and disadvantages,” said Perkin.
“My aim is to make the design available to as many people as possible in both, developed and developing countries so that anybody can build it for themselves at minimum costs as most of the structure is made from off the shelf materials and components.”
Too Good To Be True? What Facts are Missing?
Seasoned builders know that the shell of a structure is just part of the total cost. Beyond the ‘skin’ of a prefabricated design, such as this one, are elements such as labor plus:
- plumbing,
- wiring,
- cabinetry,
- finish work,
- floor coverings
and more. As any housing professional who looks objectively at this proposed project will note, none of those bullet items mentioned in any of Perkins’ promotional pieces. When MHProNews contacted Perkins to ask him – are those items priced into this design?
Silence. No replies. Potential investors – caveat emptor.
As one of our tag lines proclaims, “We Provide, You Decide.” ©
The Daily Business News has covered the progression of modular and tiny homes recently, including “flat pack” modular homes being presented as a potential solution to the U.K. housing crisis. That story is linked here. ##
(Image credits are as shown above.)

Submitted by RC Williams to the Daily Business News for MHProNews.