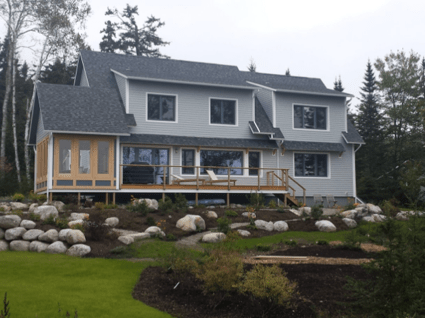
In a period of rapid innovation, anything and everything, including the manufactured housing industry, is ripe for disruption. For Ecocor, a construction firm that manufactures, delivers and assembles high-performance buildings, they hope that their time is now.
MHProNews has learned that from the company that has started production on what they dub as the first Prefabricated Passive House, designed by Richard Pedranti Architect (RPA), a full service architecture firm, focusing on sustainable design.
Earlier this year, Ecocor and RPA announced their partnership to design and build Prefabricated Passive Houses and released their Solsken Line of model homes.
Elizabeth Scott, a jewelry artist who grew up in what she calls a “post and beam passive solar house,” is the first owner of the new home.
“After growing up in my parent’s passive solar house, I always felt that it was too bad that the passive solar building technology did not develop further in the United States, until recently,” said Scott.
“I was ecstatic to find that RPA|Ecocor’s Solsken Line of prefabricated Passive Houses employed 21st century building technology and quality materials, like foam-free, dense packed cellulose insulation. I was even more convinced that it had been worth my wait when I began working with RPA to customize the design of my home.”
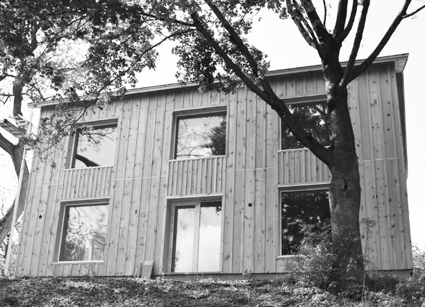
Smith’s customized Passive House is one and a half stories and features four bathrooms and three bedrooms.
“Elizabeth was Ecocor and RPA’s ideal first customer,” said Chris Corson, founder and technical director of Ecocor.
“Her passion for a modern high performance home was apparent from the first time we sat down, and she showed an eagerness to work with us to ensure that RPA|Ecocor delivered her perfect Passive House.”
RPA|Ecocor expects the entire process for homes to take six to eight months, with RPA’s computerized building models automatically providing instructions to the AB saw and production line inside the Ecocor facility, where the panelized wall and roof components are created.
Once fabricated, the panels will be loaded onto trucks and shipped to the site, which has been prepared for assembly. RPA’s design team, along with Ecocor’s construction crew, then work with local building partners to assemble the home, which is a two-week process.
Impact on the Manufactured Housing Industry?
Companies and projects like the one from RPA|Ecocor present a “looking glass” moment for the manufactured housing industry, as new technologies could possibly could result in more competition. While this particular system isn’t one that competes in price with manufactured housing today, there are others we are tracking that in just a few years could prove to be a direct challenger.
Consultant and trade publisher, L. A. “Tony” Kovach has periodically warned the industry about the possible threats that are a direct result of low-volume sales.
The Manufactured Housing Association for Regulatory Reform (MHARR) has also spoken to the opportunity that exists for the manufactured housing industry, saying in part “the MH industry must take advantage of the Trump administration’s opportunities to attain the goal of producing hundreds of thousands of HUD code homes annually.” More from MHARR, at this link here.
You can find more on the topic of items that Titus Dare, SVP of Eagle One Financial, notes are barriers for doing more manufactured home business at this link here. ##
(Image credits are as shown above.)

Submitted by RC Williams to the Daily Business News for MHProNews.