Helium isn’t just for balloons or used to make young teen voices sound funny. Helium is used in welding and in an array of other uses, a partial list of which will be provided below. Welding occurs in every manufactured housing industry frame shop. So, it is one of several essential elements of the HUD Code manufactured housing industry. Prior to this Minnesota discovery, the domestic production of helium was in decline in the U.S., and American dependency on foreign sources was looming. Along with the recent discovery in Wyoming of rare earth minerals, this helium announcement can lead to more jobs and a potential for a stable domestic supply of this “noble gas.” So, the announced discovery of a major U.S. find of helium by Canadian based Pulsar Helium Inc. in Minnesota before pivoting into more insights on helium let’s consider some other factors that should be import and understood by manufactured housing pros.
Left-leaning CBS and Yahoo News are among the mainstream media that promoted the find, which Pulsar Helium Inc.’s press release (part of which is provided below). CBS said: “Helium discovery in northern Minnesota may be biggest ever in North America.”
- Part I of today’s report will be excerpts from CBS and Yahoo’s report on the topic.
- Part II will include excerpts from Pulsar Helium’s press release.
- Part III will include some manufactured housing industry related insights, facts, and analysis.
Part I “Helium discovery in northern Minnesota may be biggest ever in North America.”
Thomas Abraham-James, CEO of Pulsar Helium, said the confirmed presence of helium could be one of the most significant such finds in the world.
“There was a lot of screaming, a lot of hugging and high fives. It’s nice to know the efforts all worked out and we pulled it off,” Abraham-James said.
CBS News Minnesota toured the drill site soon after the drill rig first broke ground at the beginning of February. The discovery happened more than three weeks later at about 2 a.m. Thursday, as a drill reached its depth of 2,200 feet below the surface.
According to Abraham-James, the helium concentration was measured at 12.4%, which is higher than forecasted and roughly 30 times the industry standard for commercial helium.
“12.4% is just a dream. It’s perfect,” he said.
For decades, the U.S. was the leading exporter of helium, but the former government-run reserves have since been depleted and sold off to private equity. Abraham-James and other researchers have since scoured the globe for other helium deposits to help improve global supply.
Prior to arriving in Minnesota, Abraham-James was working in Tanzania, where another helium discovery was made, but at half the concentration as found in the Iron Range. Russia and Qatar are other major helium exporters.
…
“It’s not just about drilling one hole, but now proving up the geological models, being able to get some really good data that wasn’t captured in the original discovery,” he explained. “It has the potential to really contribute to local society.”
The company said the feasibility study could take until the end of the year to complete. ##
Part II
VANCOUVER BC / ACCESSWIRE / February 23, 2024 / Pulsar Helium Inc. (TSXV:PLSR) (“Pulsar” or the “Company“) announces that drilling of the Jetstream #1 appraisal well* at the Topaz helium project in Minnesota is ongoing and total depth (TD) has not yet been reached. The drill time is longer than anticipated due to drilling fluid losses preventing fluid circulation and the recovery of gas and drill cuttings to the surface. The Company has therefore made the decision to pivot from drilling with water, to drilling with air; and an air package has been mobilised that will be connected to the contracted drill rig. While the delay is unfortunate, the Jetstream #1 well is still anticipated to reach TD, be tested with a comprehensive suite of open-hole wireline logs and be completed by the first week of March.
Since the spud date, the Jetstream #1 site has been visited by local Minnesota news agencies and a film crew from Reuters, collecting footage and conducting interviews that will be utilized in their upcoming Global Health 2024 documentary series. Many key local stakeholders including government officials, local residents, contractors and potential customers have toured the site.
As per the State of Minnesota’s exploratory boring regulations, Jetstream #1 is regulated by the Minnesota Department of Health who also visited site, with Jetstream #1 being in full compliance with the State’s regulations.
* In the State of Minnesota, the regulatory term is ‘exploratory boring’.
About Pulsar Helium Inc.
Pulsar Helium Inc. is listed on the TSX Venture Exchange with the ticker PLSR. It is dedicated to defining and developing primary helium assets. Its portfolio consists of the Topaz helium project in Minnesota, USA and the Tunu helium project in Greenland. Pulsar is the first mover in both locations with primary helium occurrences identified at each. Topaz is the Company’s flagship, having been drilled and flowing a remarkably high helium concentration of 10.5%. For further information visit https://pulsarhelium.com and follow us on X https://twitter.com/pulsarhelium?lang=en and LinkedIn https://ca.linkedin.com/company/pulsar-helium-inc. …##
Note: MHProNews is not taking a position or recommendation on this company for investment purposes, this report is for manufactured housing industry focused reporting.
Part III – Additional Information with More MHProNews Analysis and Commentary in Brief
1) It has been some time since MHProNews has paused to note some of the components that go into manufactured home construction. Thousands of manufactured housing pros have never stepped foot into a manufactured home production center (a.k.a.: factory, plant, building center, etc.). It is useful to know more about the industry you are working in, or for investors/public officials, researchers, and others to consider what is required to build a HUD Code manufactured home. This discovery of helium in Minnesota is a useful pivot point to that broader topic.
2) Per the HUD website (italics added): “The HUD Code, unlike conventional building codes, requires manufactured homes to be constructed on a permanent chassis.”
3) As MHProNews has previously reported, there are efforts underway to change that permanent chassis requirement to make a removable chassis requirement. That is not a new initiative, it is one that what is now called the Manufactured Housing Association for Regulatory Reform (MHARR) sought in the early 1990s.
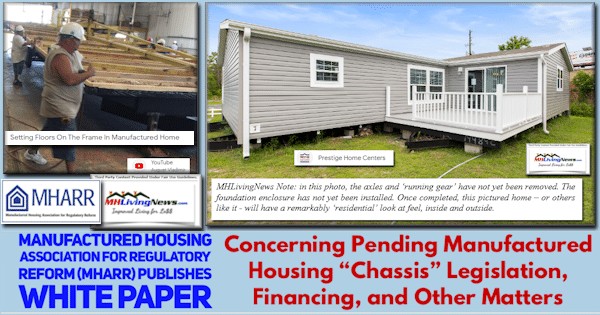
4) In order to make a frame/chassis for a HUD Code home, welding is required. So, this find of helium has a directly connection to what occurs in manufactured housing frame shops. This factory tour by Jacobsen shows the frame welding starting just before the 2-minute mark.
5) Per a Q&A with left-leaning AI powered Copilot, are the following.
> “In a different Q&A, Copilot identified helium as necessary for welding which is used in manufactured housing frame/chassis fabrication. Elaborate on that point, and link results.”
> “Useful. Provide a list of components that go into every HUD Code manufactured home, including major items like lumber, but also some of the items that people may not normally think about.”
- Lumber and Structural Materials:
- Framing: The home’s wooden frame provides structural support. It includes studs, joists, rafters, and beams.
- Flooring: Plywood or oriented strand board (OSB) forms the base for the home’s floors.
- Roofing Materials: Roof trusses, sheathing, and roofing materials (shingles, metal panels, etc.) are essential.
- Insulation and Energy Efficiency:
- Insulation: Various types of insulation (fiberglass, foam, etc.) are used in walls, ceilings, and floors.
- Windows and Doors: Energy-efficient windows and insulated doors contribute to thermal comfort.
- Interior Components:
- Drywall or Paneling: Interior walls are covered with drywall or decorative paneling.
- Cabinetry and Fixtures: Kitchen and bathroom cabinets, sinks, faucets, and toilets.
- Floor Coverings: Carpet, vinyl, or laminate flooring.
- Electrical and Plumbing Systems:
- Wiring and Outlets: Electrical wiring, outlets, switches, and light fixtures.
- Plumbing: Pipes, fixtures, water heaters, and sewage systems.
- HVAC: Heating, ventilation, and air conditioning systems.
- Exterior Features:
- Siding: Vinyl, wood, or other siding materials.
- Skirting: The material that encloses the space beneath the home.
- Doors and Windows: Exterior doors, windows, and their frames.
- Safety and Compliance Components:
- Smoke Detectors and Alarms: Required for safety.
- Fire Extinguishers: For emergency fire response.
- Certification Label: The red label indicating compliance with HUD standards.
- Less Obvious Components:
- Anchoring System: Used to secure the home to the ground.
- Transportation Components: The chassis, axles, and wheels used during transportation.
- Tie-Downs: Straps or anchors securing the home to the ground after installation.
Remember that each component plays a crucial role in the overall functionality, safety, and comfort of a manufactured home. Whether it’s the visible finishes or the hidden infrastructure, all these elements contribute to a well-built and compliant dwelling. 🏠🔨
For more detailed information, you can refer to the HUD Manufactured Housing and Standards FAQ….”
7) MHProNews has previously reported on the find of rare earth minerals, which can play a role in higher tech items and could cause a need for housing near the mining sites.
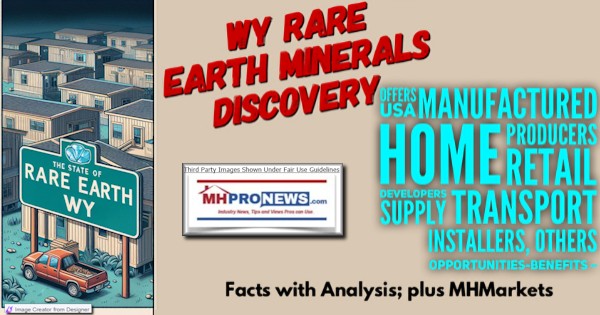
8) MHProNews has also reported on the tension between those who want to ship into the U.S. components and appliances for manufactured housing from China or elsewhere, and those who would rather see those items produced domestically.
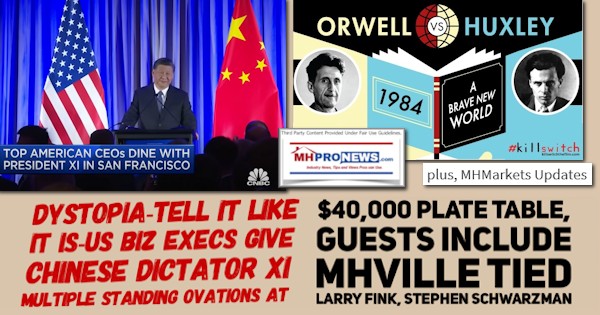
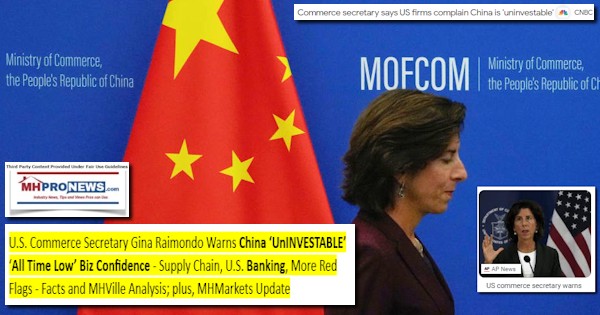
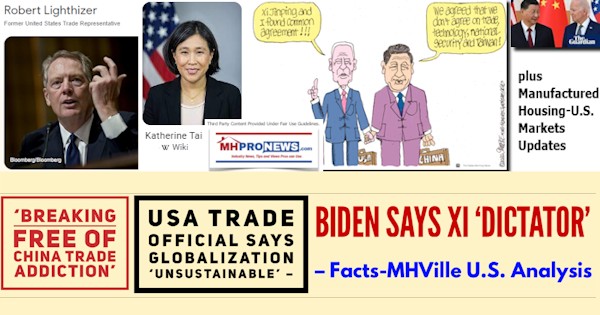
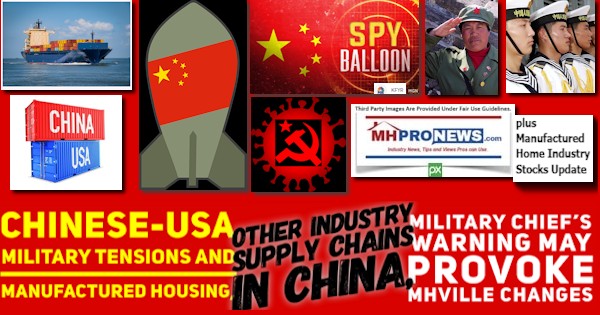
9)
> “Safety, energy, structural standards and components required for HUD Code manufactured homes.”
> “Many people don’t realize that the HUD Code for manufactured homes is a performance-based code rather than a prescriptive code, like is common in conventional housing. Explain the differences, and how that performance-based standard can lead to innovation in affordable, quality, housing. Also note the unique dispute resolution program that is not common among far more costly conventional housing.”
- Performance-Based vs. Prescriptive Codes:
- Prescriptive Codes:
- Prescriptive codes provide specific instructions for the type, size, spacing, and connections of building components.
- They dictate precisely what materials and methods to use.
- For example, a prescriptive code might specify the exact thickness of insulation, the type of wiring, or the dimensions of structural members.
- These codes are often rigid and may not accommodate new materials or innovative techniques easily.
- Conventional housing typically adheres to prescriptive codes.
- Performance-Based Codes:
- Performance-based codes focus on achieving specific outcomes or performance goals.
- Instead of dictating specific methods, they set performance criteria that must be met.
- Builders have flexibility in choosing materials and methods as long as they achieve the desired performance.
- This approach encourages innovation, as it allows for creative solutions that meet or exceed performance requirements.
- The HUD Code for manufactured homes follows a performance-based approach.
- Prescriptive Codes:
- HUD Code and Innovation:
- The HUD Code’s performance-based nature has several benefits:
- Flexibility: Manufacturers can explore new materials, construction techniques, and design approaches to meet performance goals.
- Affordability: By focusing on outcomes rather than rigid specifications, the HUD Code allows cost-effective solutions.
- Quality: The code emphasizes durability, safety, and energy efficiency, ensuring that manufactured homes maintain their value over time.
- Energy Efficiency: Performance-based standards encourage energy-efficient designs, promoting sustainability.
- Durability: The HUD Code addresses the durability of components like doors, windows, and roofing materials, ensuring long-lasting homes.
- Innovation: Manufacturers can experiment with innovative features, such as smart home technology, efficient HVAC systems, and advanced insulation.
- Adaptability: As technology evolves, the HUD Code can incorporate new standards without major overhauls.
- Customization: Builders can tailor homes to regional climates and homeowner preferences while meeting performance benchmarks.
- The HUD Code’s performance-based nature has several benefits:
- Dispute Resolution Program:
- The HUD Code includes a unique Dispute Resolution Program (DRP):
- Purpose: The DRP resolves disputes among manufacturers, retailers, and installers regarding defects reported within the first year after installation.
- Process: Homeowners can report defects, and the program facilitates mediation or nonbinding arbitration.
- Timeliness: Quick resolution ensures homeowners receive necessary corrections promptly.
- Financial Risk Mitigation: By addressing defects early, the program reduces financial risks for FHA-insured loans.
- Not Common in Conventional Housing: Unlike conventional housing, which lacks a standardized dispute resolution process, the HUD Code’s DRP provides clarity and fairness.
- The HUD Code includes a unique Dispute Resolution Program (DRP):
In summary, the HUD Code’s performance-based approach encourages innovation, affordability, and quality in manufactured homes. Its unique dispute resolution program ensures timely solutions for homeowners. 🏠✨ …”
A case can be made that the more items that are domestically sourced, the better it is for manufactured housing supply chains and for the country in general. The discovery of helium could produce more useful ripple effects for America in general and for manufactured housing. For additional information see the linked reports. ###
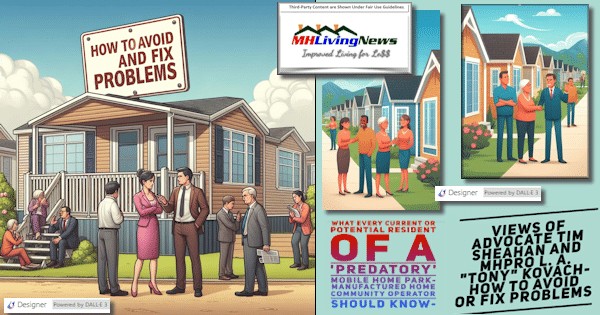
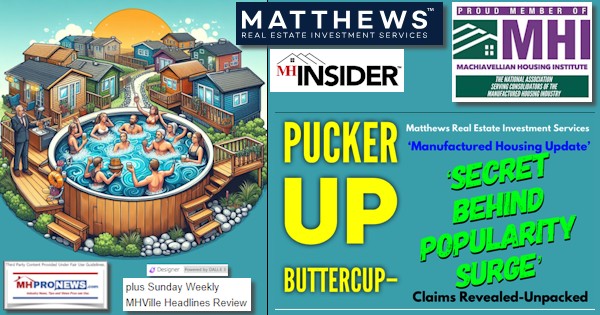
Tipsters? Forward or Submit items at this link here.
Employees of a “predatory” MHI brand? Click here.
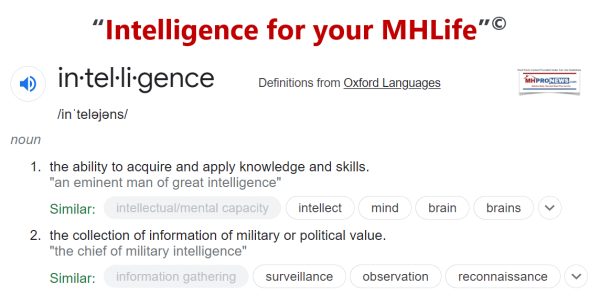
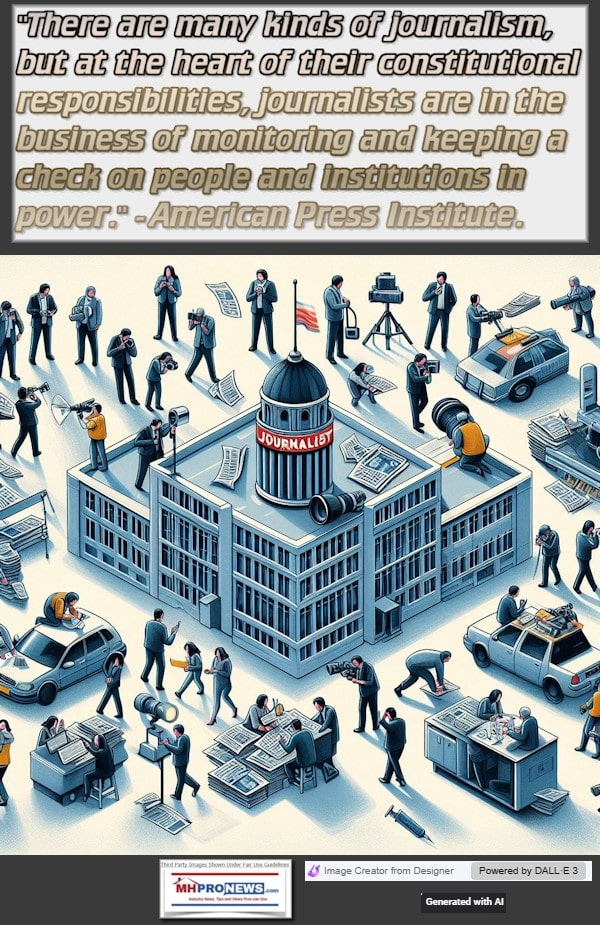
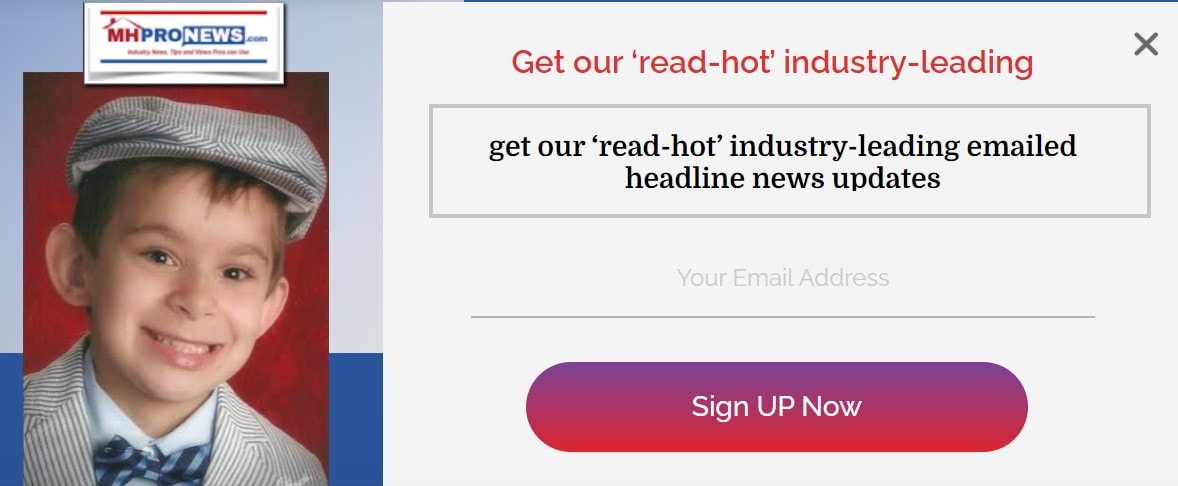
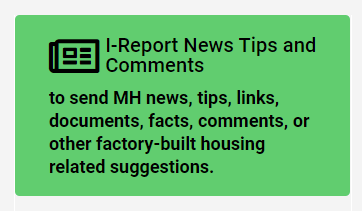
Again, our thanks to free email subscribers and all readers like you, as well as our tipsters/sources, sponsors and God for making and keeping us the runaway number one source for authentic “News through the lens of manufactured homes and factory-built housing” © where “We Provide, You Decide.” © ## (Affordable housing, manufactured homes, reports, fact-checks, analysis, and commentary. Third-party images or content are provided under fair use guidelines for media.) See Related Reports, further below. Text/image boxes often are hot-linked to other reports that can be access by clicking on them.)
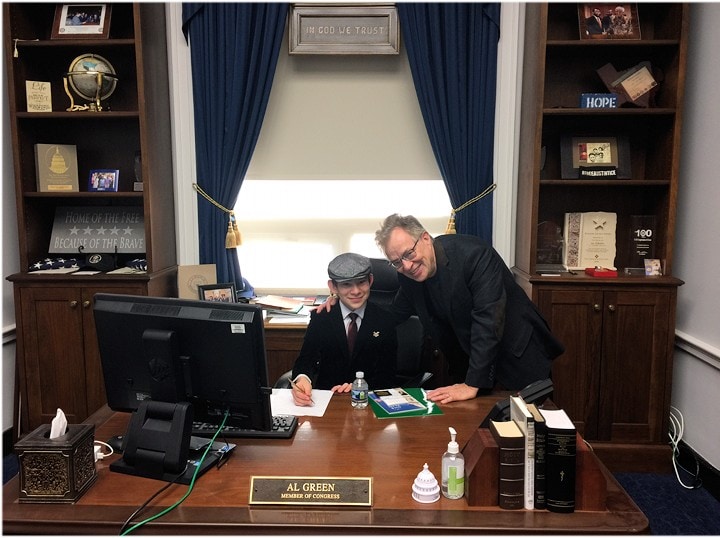
By L.A. “Tony” Kovach – for MHProNews.com.
Tony earned a journalism scholarship and earned numerous awards in history and in manufactured housing.
For example, he earned the prestigious Lottinville Award in history from the University of Oklahoma, where he studied history and business management. He’s a managing member and co-founder of LifeStyle Factory Homes, LLC, the parent company to MHProNews, and MHLivingNews.com.
This article reflects the LLC’s and/or the writer’s position and may or may not reflect the views of sponsors or supporters.
Connect on LinkedIn: http://www.linkedin.com/in/latonykovach
Related References:
The text/image boxes below are linked to other reports, which can be accessed by clicking on them.’
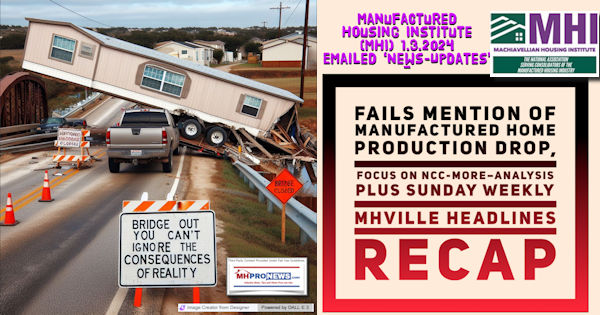
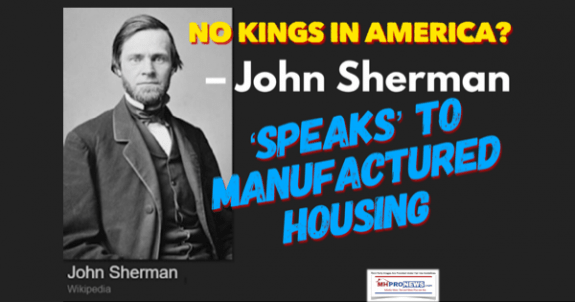
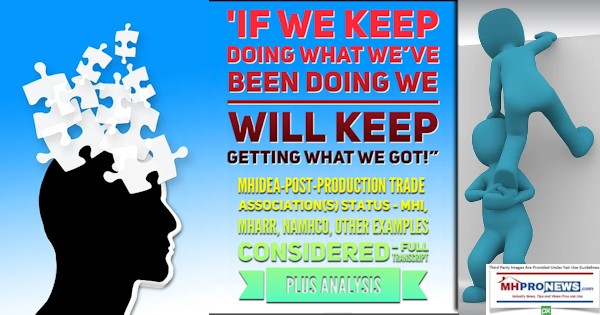
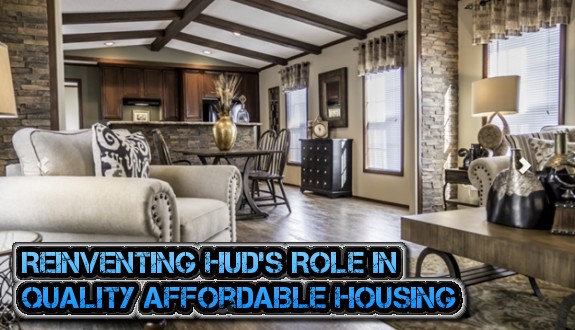